LEARN MORE ABOUT US
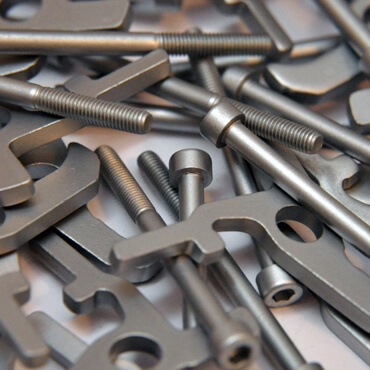
Located at Ambattur, Chennai, Tamilnadu, we NG Coaters are engaged in Providing Solutions to Corrosion Wear and Lubrication. Our products keep the equipment and machinery in optimum working conditions. Moreover, these also enhances working life, productivity and profitability along with decreasing maintenance costs and downtime.
Our quality controllers conducts rigorous quality testing on well defined quality parameters to ensure a flawless product range at clients end. We also offer our products at industry leading prices without compromising on quality. Our quality centric, client oriented, transparent and flexible business approach has made us capable of catering to industry segments.
Zinc Flake Coating, Zinc Aluminium Flake Coating, Aluminium Flake Coating, Zinc and Aluminium Flake Coating, Dip & Spin Coating, Dip Spin Coating, Electroplating.
We have the state of art dip spin coating facility combined with baking furnace. The output of dip spin facility is 200 Kg per hour The dipspin coater is PLC controlled with programmable sequencing steps to provide uniform coating thickness consistently on all intricate surfaces of the component.
Dip coating uses plastics that harden and maintain their shape when heat-treated. The process of plastic coating is not limited by object size or dimension, as the container holding the coating can be designed to accommodate larger or smaller products for full coverage. There are three basic steps to the process.
Spin coating is a widely used and versatile technique for depositing materials onto substrates with accurate and controllable film thicknesses. Spin coating uses the centripetal force and surface tension of the solution to create an even film, making it quicker than other thin film coating methods.
The dip-spin coating process consists of cleaning, application, and curing. The parts are first cleaned and then pretreated to remove oxides. Once the pretreatment dries, we place them in the wire mesh basket and then submerge in the coating solution.
Dip Spin is method of applying a thin coating on small parts using centrifugal force to control film thicknesses. The force generated by the high rate of basket speed allows for consistent, even coating in a short period of time. As the spinning process ends the basket begins to slow and is removed from the rotating chamber while still in motion. This allows for the paint or coating to safely drain from the parts and basket.
Dip spin coating systems serve for the coating of mass goods in an efficient way, which are dipped in liquid coating materials either in baskets or racks depending on the range of parts.
Dip-spin coating has a number of benefits for your products:
Follow Us On
Facebook,
Twitter,
Instagram,
Google My Business,
Google My Business Website,
Bing,
Yahoo
Monday | Open 24 Hours |
Tuesday | Open 24 Hours |
Wednesday | Open 24 Hours |
Thursday | Open 24 Hours |
Friday | Open 24 Hours |
Saturday | Open 24 Hours |
Sunday | Open 24 Hours |
Get Your FREE Quote Today!
We are available 24/7 email or telephone. Call or Text!